Products emerging from aerosol machines have become an indispensable part of modern life. The wide range of applications for these products, from spray paints and deodorants to food products and pharmaceuticals, highlights the critical importance of quality control in production processes. Since they are pressurized containers, even the slightest production error can pose serious safety risks. Therefore, rigorous quality control processes in aerosol production are essential to ensure consumer safety and guarantee product effectiveness. Additionally, compliance with legal regulations and maintaining brand reputation are indispensable outcomes of an effective quality control system.
What Stages Does the Quality Control Process in Aerosol Production Cover?
A comprehensive quality control process in aerosol production encompasses all stages from raw materials to the final consumer. This process generally consists of the following steps:
-
Raw Material Inspection: Ensuring that all components used in production (active ingredients, solvents, propellants, packaging materials, etc.) meet specified quality standards.
-
Filling Control: Checking whether the correct amount of product and propellant gas is filled into aerosol cans. In this stage, checkweighers play a crucial role.
-
Leakage Control: Inspecting filled and sealed aerosol cans for any leaks. Leak detection devices are used for this purpose.
-
Functional Testing: Ensuring that the spraying mechanism functions correctly and that the spray pattern and amount meet the set standards.
-
Packaging and Labeling Control: Verifying that labels are correctly and completely placed, packaging is intact, and information such as expiration dates is accurate.
-
Final Product Testing: Random sampling of finished products for various tests (e.g., internal pressure test, weight control, leakage test, spray test, etc.). The water bath test is a commonly applied method at this stage.
Why Should Aerosol Filling Weight Be Controlled? What Is the Role of Checkweighers?
Ensuring the correct filling weight in aerosol products is crucial to protecting consumer rights and guaranteeing product effectiveness. Underfilling fails to meet consumer expectations, while overfilling poses safety risks. Checkweighers eliminate this risk by automatically checking the weight of each aerosol can in high-speed production lines. Products outside the specified tolerance range are automatically rejected by the system, preventing defective products from reaching the market. These machines enhance production efficiency while maintaining quality standards.
Why Is Leakage in Aerosols Dangerous? How Do Leak Detection Devices Work?
The pressurized nature of aerosol products increases the risk of leakage. A leak can lead to a reduction in product content, loss of propellant gas, and ultimately, the product becoming non-functional. More importantly, aerosols containing flammable or explosive substances can pose severe safety hazards in case of leakage. Leak detection devices are a critical part of the production line to minimize these risks. These devices typically operate by using sensors that detect pressure changes around aerosol cans or specialized gas detectors. Products with detected leaks are immediately removed from the line and safely disposed of.
Why Is the Water Bath Test Performed on Aerosols? How Does This Test Work?
The water bath test is a widely used method to check the quality and safety of aerosol products. In this test, filled and sealed aerosol cans are submerged in water at a specific temperature (usually around 50°C) for a set duration (typically 3-5 minutes). This process increases the internal pressure of the aerosol can. If there are any weak points, micro-cracks, or defective seals, a leak will occur under this pressure. Cans emerging from the water bath are observed, and any leaking products are identified and removed, preventing faulty items from reaching the market.
What Other Methods and Machines Are Used for Quality Control?
In addition to the main machines mentioned, other methods and equipment are used to ensure quality in aerosol production. Visual inspections are conducted on the production line to detect packaging defects, labeling errors, or other physical flaws. Functional tests verify that the spray mechanism operates correctly. Additionally, in some cases, laboratory analyses such as gas chromatography are used to examine product composition and propellant quality in detail.
How to Establish an Effective Quality Control Process? Why Is Compliance with Standards Important?
To establish an effective quality control process, clear quality standards must first be defined and strictly followed throughout all production stages. Quality control procedures should be documented in writing, and all personnel should be trained accordingly. Additionally, all quality control machines must be regularly calibrated and maintained. Compliance with international quality standards (e.g., ISO 9001, GMP) is a critical step in enhancing the effectiveness of quality control in aerosol production and ensuring adherence to legal regulations.
Why Is Quality Control in Aerosol Production Important? What Are the Future Trends?
Quality control in aerosol production is not just a legal requirement but also an essential factor for consumer safety and brand success. Checkweighers, leak detection devices, and water baths play a crucial role in ensuring consistent and reliable quality control in production lines. In the future, automation and artificial intelligence technologies are expected to be further integrated into quality control processes. This will lead to faster, more accurate, and more efficient quality control systems, further enhancing the quality and safety of aerosol products.
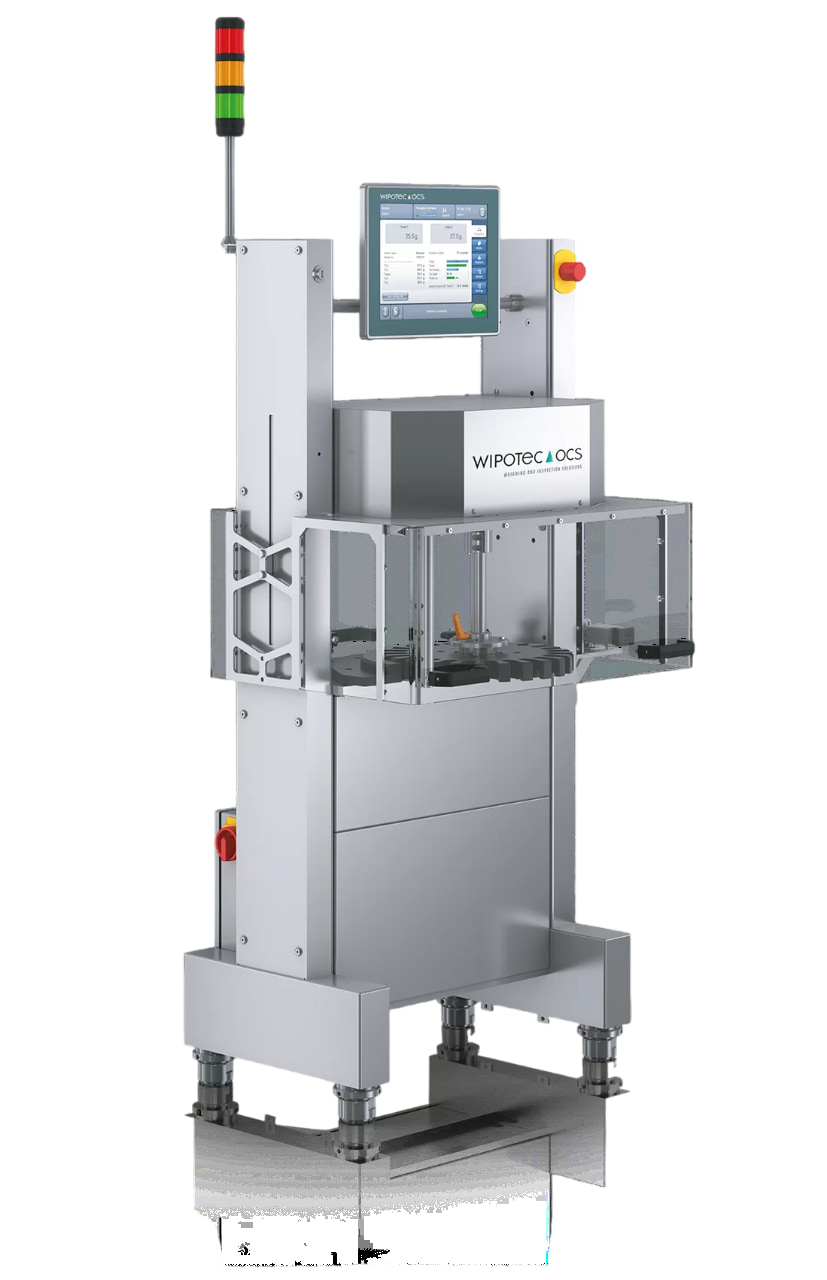