What is an Aerosol Filling Line and How Does it Work?
An aerosol filling line at its core is basically different equipments which are contrubuting to different operations connected. Each operation is done via different part of the line. As an example an aerosol line has 2 different filling units. One is for the liquid product and the other is for propellant gas. For placing operations we place the valve inside empty cans. We place the actuator after the product is filled and lastly we place the cap on top. To dive into more details, filling material is usually some type of liquid mixture along with flavor. As per propellant gas, the gas type commonly used in aerosol filling field is LPG, more deeply propane-butane mixture.
Each equipment in the aerosol filling line plays a dedicated role in the overall system. The line is typically linear or rotary and is composed of stations that handle specific tasks like can feeding, liquid filling, crimping, gas filling, leak testing, actuator placement, and capping. The integration between these units ensures a smooth and continuous flow, minimizing human intervention. A critical aspect of this process is synchronization. If one unit is slower than the others, it can become a bottleneck and reduce the line’s overall efficiency.
For example, during the gas filling phase, extreme caution must be taken as LPG is highly flammable. Specialized nozzles and precision timing are used to inject the correct amount of gas into each canister without waste or hazard. In most modern setups, sensors constantly monitor temperature, pressure, and flow to ensure consistent quality.
Which Equipment is Necessary for an Aerosol Filling Line?
If you are at the stage of equipment selection in aerosol filling field, must to have operations are liquid filling, crimping and gas filling since these steps can not be done manually. Even if that is doable, mostly is not energy efficient. Another thing to keep in mind is product or propellant is mostly flammable. This requires further safety measures to keep in mind. As someone who has worked in the field for long time, another equipment that is not a must but for me one that a producer should have is called gas house. Gas house is a metal container specifically created to ensure propellant filling machines filling environment. Has improved security interms of both fire and explosion risk.
Besides the core filling equipment, additional machinery such as checkweighers, leak testers, labeling machines, and palletizers are commonly integrated. These machines help improve the accuracy, safety, and traceability of the product. For high-output facilities, rotary filling lines offer significantly faster operation compared to linear systems, and servo-based filling valves allow programmable dose sizes for different products.
Another crucial factor is whether you’re producing flammable or non-flammable aerosols. If you’re handling flammable gases, explosion-proof (ATEX) components become mandatory. The gas house plays a central role here—it’s not just a protective cage, it’s a safety buffer zone designed to isolate the explosive zone from operators and electrical panels, often equipped with ventilation systems, flameproof lighting, and automatic shutdown alarms in case of leaks.
How is Hygiene and Cleaning Ensured in an Aerosol Filling Line?
We have standart cleaning procedure, this ensure cleanliness and hygiene level fort he filling line. If the user is looking for elevated hygiene levels, they can send samples to laboratories to check if there is any contamination. Generally aerosol lines are washed with high concenteration alcohol or pure water depending on the product type. General hygiene of the line is kept this way. Deep cleaning level we can offer CIP modules for our fillers. Usage of 316 Stainless steel material is also preventive against contamination and provides enhanced hygiene levels.
Hygiene is not just about visible cleanliness—it’s a matter of consumer safety and product shelf life. Depending on whether you are filling personal care, household, or pharmaceutical aerosols, the hygiene requirements may differ significantly. For sensitive applications like nasal sprays or medical-grade aerosols, you might need ISO-classified cleanroom environments. Here, HEPA filters, laminar airflows, and UV sterilization modules may also be included in the production room setup.
CIP (Clean-in-Place) modules, mentioned above, are particularly useful because they automate the internal cleaning of pipelines and tanks, ensuring that every corner of the equipment gets sanitized without disassembly. This also reduces downtime and improves productivity between batch changes. Additionally, using 316L stainless steel, known for its corrosion resistance, provides a long-term hygienic solution, especially when aggressive cleaning agents like ethanol or peracetic acid are used.
What are the Safety Measures in an Aerosol Filling Line?
At it’s core an aerosol line should be correspondant to FEA guidelines and EN-60079-10-2. What this means is global organizations and governments already considered many things and created guidelines and directives to this. Our aerosol filling lines are designed considering all these points. Another important point on this topic is using ATEX graded equipment, but that alone can not provide the required safety. In these guidelines and directives you can also find how to improve efficiency, continuity and how to maintain your filling Warehouse properly.
Safety measures in an aerosol filling environment span across multiple layers: electrical, chemical, and mechanical. FEA (Fédération Européenne des Aérosols) provides the industry-wide safety standards. These cover aspects like maximum allowable gas content, burst resistance of cans, and pressure thresholds.
EN-60079-10-2 refers specifically to explosive atmospheres and how to classify and control them in manufacturing environments. These regulations demand detailed zoning of the plant—where Zone 0, 1, or 2 indicates increasing levels of explosion risk. These zones must be equipped with sensors for gas leaks, emergency shut-off systems, flame arrestors, and explosion-proof junction boxes. Moreover, operational staff must be trained periodically on emergency procedures, and drills should be conducted to ensure a fast and coordinated response in case of hazard.
Which Process Improvements Should Be Made to Increase Efficiency?
Firstly a smart layout is very important. There should be no cross movement in the Warehouse. Where the raw material comes and where the finished goods go should be planned accordingly to prevent any traffic. Production planning and production optimization should be done previously to ensure efficiency. There is nothing worse than waiting for product mixer to finish in between products. Entire process is interconnected, that is why for an increasing efficiency all these steps should be taken into account.
The layout isn’t just about physical flow; it’s also about time and data flow. A lean layout saves not just steps, but also decisions. It allows the operators to work with clarity and less confusion. One improvement many companies benefit from is digital production dashboards showing current machine status, product counts, and error logs. This provides instant visibility into inefficiencies.
Moreover, adopting predictive maintenance can also help reduce unplanned downtimes. Instead of reacting to breakdowns, sensors and data analytics can forecast when a component is likely to fail, allowing for planned interventions that don’t disrupt production.
How is Energy Efficiency Ensured in the Setup of an Aerosol Filling Line?
Energy type we mainly use in filling lines is air. Machines operate mostly with air and a lot of it. Since we generate the air with a compressor, air is related to electricity bills. To increase energy efficiency of our lines, we systematically invite manufacturers of pneumatic equipments and discuss the air usage and how to improve it.
Air leaks are a silent killer of energy efficiency in aerosol lines. A tiny leak in a pneumatic tube may seem trivial, but over the course of a month, it can result in hundreds of euros in energy waste. This is why regular leak detection and air pressure auditing are critical.
Beyond just the air, motors, pumps, and lighting systems can be selected with high-efficiency grades (IE3 or IE4 class motors). Using variable frequency drives (VFDs) on conveyors and mixers also allows machines to adjust power usage based on demand instead of running at full speed unnecessarily.
Energy monitoring systems that track kilowatt-hour usage per batch or shift can provide insights on when and where energy spikes occur. With these insights, production can be scheduled to optimize compressor cycles or reduce simultaneous energy-intensive tasks.
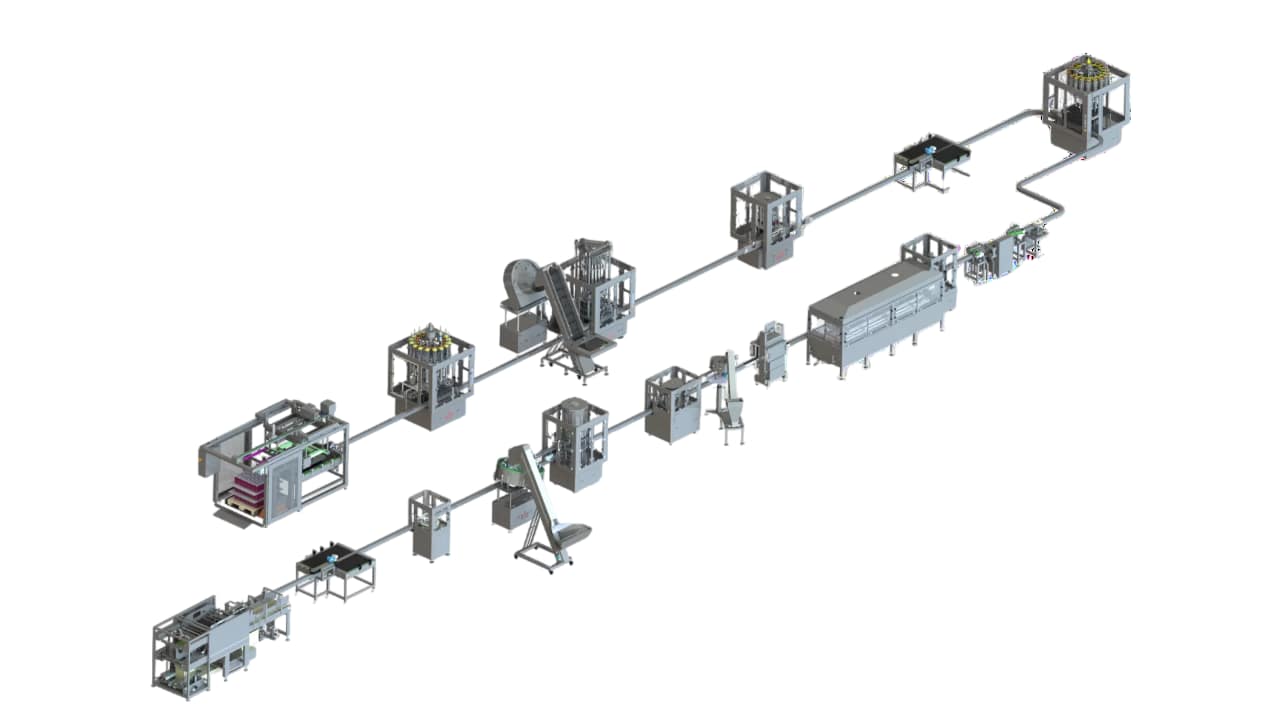