In the world of aerosol production, choosing the right filling system is more than just a technical decision—it’s a strategic one. Whether you’re running a fast-paced line or just entering the game, understanding the difference between automatic and semi-automatic filling systems can shape how efficiently (and profitably) you scale.
Let’s walk through what actually matters when comparing these systems—not just the specs, but the logic behind choosing one over the other.
The Importance of Filling Systems in Aerosol Production
At the heart of every solid aerosol packaging setup lies one thing: your filling technology. It determines your line speed, consistency, product safety, and how scalable your production really is.
It doesn’t matter if you’re filling deodorant, brake cleaner, or air freshener—if your aerosol filling system is inconsistent or slow, you’ll face issues with waste, rework, or worse, customer returns. So yeah, the right system isn’t optional—it’s foundational.
Automatic Aerosol Filling Systems: Features and Advantages
The automatic filling system is built for efficiency and volume. These setups typically include full automation: from valve placement and crimping to gas filling and actuator mounting—all synced through a conveyor-based system.
What makes the full systems appealing to the customer?
- High production efficiency—you can hit 18,000+ cans per hour.
- Less manual labor—1–2 operators are usually enough to operate the entire line.
- Excellent consistency—great for tight tolerances and quality standards and no room for mistakes.
- Minimal human error—reduces overfilling, underfilling, safety risks and more.
That said, the upfront investment is higher, and maintenance requires skilled hands. But if you’re in mass production or want to scale up without scaling your team, automatic wins.
Semi-Automatic Aerosol Filling Systems: Features and Advantages
The semi-automatic filling system offers flexibility and a lower barrier to entry. Ideal for niche brands, contract fillers, or R&D environments—it’s all about control and adaptability.
Why choose semi-automatic?
- Lower capex—it doesn’t eat your budget in phase one.
- Easier changeovers—switch between SKUs without drama.
- Compact design—great for tighter spaces or pilot lines.
- Operator-driven—more hands-on, but also more adaptable.
While it won’t match the speed of a fully automated line, for small-to-mid runs, it often makes more sense—especially if you’re handling diverse product types or frequent changeovers.
Comparison of Automatic and Semi-Automatic Systems: Key Differences
Here’s a breakdown of how the two systems stack up:
Throughput High (18,000+ cans/hr) for fast automatics
Throughtput Medium (600–700 cans/hr)
If you’re consistently pushing volume, semi-automatic might actually cost you more in the long run via labor, slower throughput, and downtime.
Investment budget is another thing to keep in mind while planning for such investments.
Safety and others should be discussed deeply before we choose the machine for our setup.
Which System is More Suitable for Which Business? Decision-Making Criteria
So… which one’s right for you? Here’s a quick decision framework based on actual field logic—not sales decks:
Launching a new product line or entering aerosol production?
Start with semi-automatic. It keeps you agile and cost-light.
Running one or two high-volume SKUs daily?
You’ll likely need automatic systems to stay competitive on unit cost.
Need flexibility for small batch or contract jobs?
Semi-automatic gives you speed during changeovers and less waste.
Want to reduce headcount or increase consistency?
Automatic systems are built exactly for that.
Think about your SKUs, batch size, team structure, and future plans. There’s no one-size-fits-all—but there is a smart fit.
New Technologies and Future Trends
Filling technologies are evolving faster than people realize. Here’s what’s starting to hit the market—and what’s just around the corner:
Servo-controlled fillers that auto-adjust for can height and product density.
Smart diagnostics that flag issues before you even see a jam.
Integrated weighing systems for real-time fill verification.
Eco-forward aerosol packaging solutions (like bag-on-valve tech).
It’s not always just about filling faster anymore—it’s about filling smarter, cleaner, and more traceably. Safety is becoming an important topic in the field aswell.
Choosing between an automatic or semi-automatic aerosol filling system isn’t just about machine specs—it’s about your business model, your market, and where you’re headed. As a professional in the field, I always suggest my clients to opt for automatic machines due to safety risks that this business provides. Now we are more than sure that in every business main safety reliablity is human and it is best to decrease it.
So ask yourself: What does growth actually look like for me? And which system makes that smoother, not harder?
Still unsure? We’ve helped dozens of companies walk this exact path—happy to share what worked (and what didn’t).
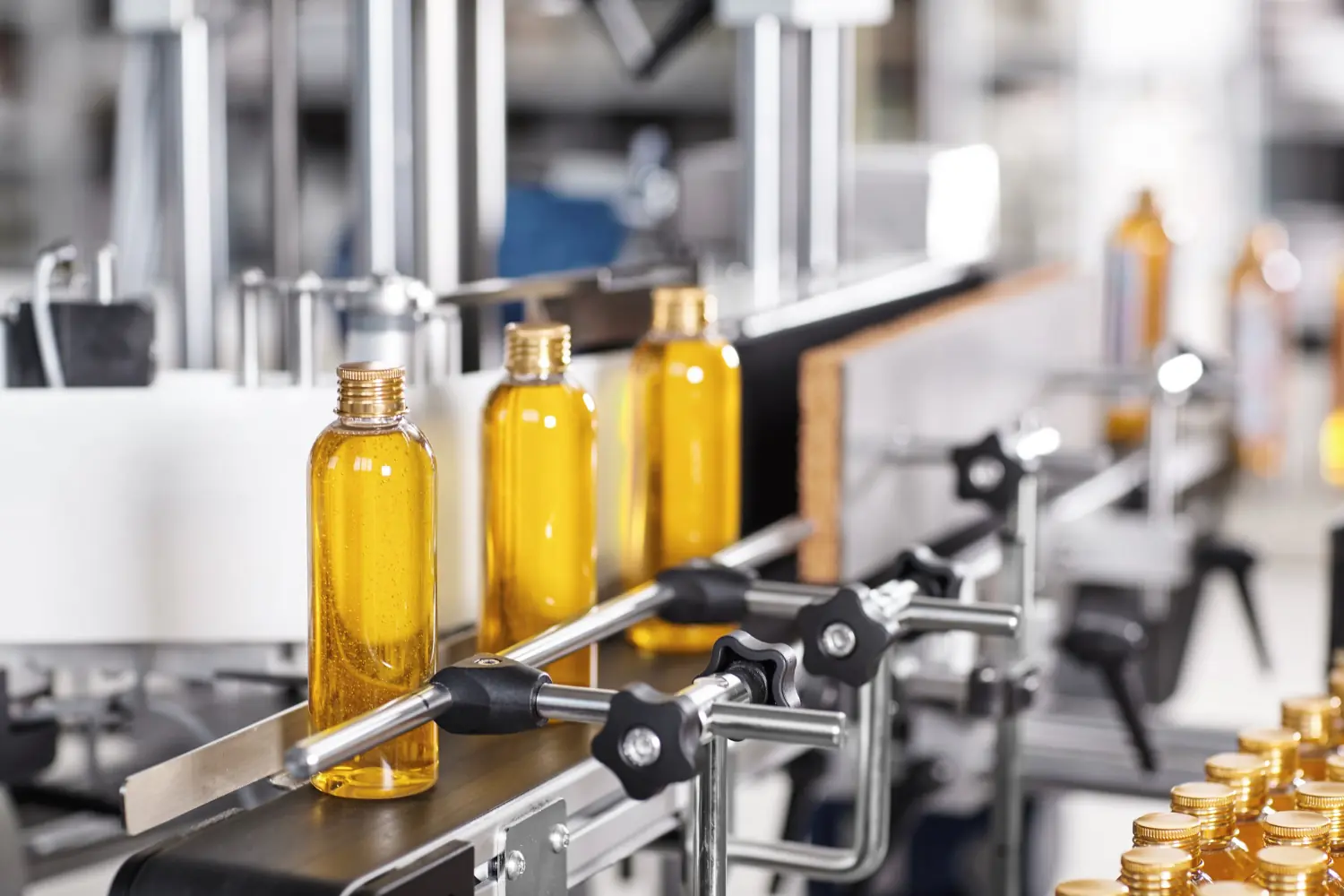