Rapidly evolving industries, liquid filling machines are a vital component in the production processes of various sectors, including food, cosmetics, pharmaceuticals, and chemicals. These machines are designed to automate and streamline the filling of liquids into containers, ensuring accuracy, consistency, and efficiency. In this article, we will explore how liquid filling machines work, their significance in various industries, and how they contribute to improving production processes.
What are Liquid Filling Machines, How Do They Work, and in Which Production Processes Are They Used?
Liquid filling machines are specialized devices that automatically dispense liquid products into containers of different sizes and shapes. These machines are essential for industries that require high levels of precision and efficiency in filling processes. They work by utilizing a variety of mechanisms, such as gravity, pressure, vacuum, or piston systems, depending on the type of liquid and container involved.
Liquid filling machines are used in various production processes across multiple industries. They are commonly found in food and beverage production lines, pharmaceutical manufacturing, cosmetic packaging, and chemical industries. In each of these sectors, these machines ensure the accurate filling of bottles, jars, tubes, and other containers, minimizing waste and ensuring uniformity in production.
How Do Liquid Filling Machines Ensure Hygiene, Safety, and Efficiency in the Food Industry?
The food industry has stringent hygiene and safety regulations due to the direct impact on consumers’ health. Liquid filling machines designed for this sector are built to meet these high standards. These machines are often made of stainless steel and other non-corrosive materials to prevent contamination. They are also equipped with systems that ensure easy cleaning, such as CIP (clean-in-place) technology.
In addition to hygiene, liquid filling machines in the food industry also improve production efficiency. By automating the filling process, these machines reduce labor costs and ensure that the filling process is completed in a timely and precise manner. This, in turn, helps to maintain consistent product quality and enhances overall productivity.
How Do Liquid Filling Machines Increase Speed, Precision, and Safety in the Chemical Industry?
In the chemical industry, liquid filling machines are crucial for handling a wide range of substances, from simple liquids to highly volatile or hazardous chemicals. These machines provide increased speed, accuracy, and safety by ensuring that the correct amount of liquid is dispensed into containers, regardless of the chemical’s viscosity or volatility.
High-precision filling systems help prevent overfilling or underfilling, which can lead to waste and unsafe conditions. Many liquid filling machines used in the chemical industry also feature enhanced safety mechanisms, such as explosion-proof motors or automatic shut-off systems, to protect workers and the environment.
What are the Sterilization and Quality Control Processes for Liquid Filling Machines in the Pharmaceutical Industry?
In the pharmaceutical industry, maintaining high standards of cleanliness, sterilization, and quality control is paramount. Liquid filling machines in this sector are designed to meet stringent regulations, including those set by the FDA and other health authorities. Sterilization processes such as steam sterilization (autoclaving) or UV light treatment are often used to ensure that the machines are free from contaminants.
Quality control is another critical aspect in pharmaceutical production. Liquid filling machines are integrated with monitoring systems that track the volume, weight, and overall quality of the filled containers. This ensures that every bottle or vial is filled accurately, meeting the necessary standards for consistency, dosage, and safety.
How Do Liquid Filling Machines Affect Product Quality, Aesthetics, and Precision in Cosmetics Production?
In the cosmetics industry, product quality and aesthetics are essential factors that determine consumer appeal. Liquid filling machines used in cosmetics production must ensure not only the precision of the filled product but also maintain the visual and physical integrity of the container and its contents.
Liquid filling machines play a significant role in preserving the quality of cosmetics by preventing air bubbles, contamination, and spillage. Additionally, these machines help ensure the precise filling of delicate products such as lotions, serums, and perfumes, maintaining their consistency and appearance, which is critical for branding and consumer satisfaction.
How Do Automation and Integrated Systems Increase Efficiency and Precision in Liquid Filling Processes?
Automation and integrated systems are transforming liquid filling processes across all industries. These systems work by connecting filling machines with other components of the production line, such as labeling, capping, and packaging machines, creating a seamless flow of operations. Automation helps to minimize human error, optimize production speeds, and maintain precision in each filling cycle.
The integration of these systems also allows manufacturers to monitor and adjust the production process in real time, which significantly reduces downtime and enhances overall efficiency. For example, automated systems can adjust fill levels or speeds based on the viscosity of the liquid, ensuring optimal performance throughout the production cycle.
Which Strategies Should Be Used to Achieve Cost Savings with Liquid Filling Machines?
To achieve cost savings with liquid filling machines, manufacturers should focus on both initial investments and long-term operational efficiency. Some strategies include:
- Regular Maintenance: Keeping machines well-maintained ensures that they run efficiently, reducing the likelihood of breakdowns and costly repairs.
- Energy Efficiency: Choosing energy-efficient machines can reduce operational costs in the long run.
- Flexible Machines: Investing in versatile machines that can handle various container sizes and liquid types reduces the need for multiple machines, saving space and costs.
- Optimizing Production Speed: Properly calibrating the filling machines to match the production speed with the liquid viscosity can help avoid waste and enhance productivity.
By adopting these strategies, manufacturers can significantly reduce operational costs while maintaining product quality and consistency.
What are the Environmental Impacts of Liquid Filling Machines, and Which Solutions Are Available for Sustainable Production?
Like all industrial equipment, liquid filling machines have environmental impacts. These include energy consumption, waste generation, and the use of resources in production. However, several solutions can mitigate these effects and support sustainable production practices.
- Energy-Efficient Machines: Newer models of liquid filling machines are designed to consume less energy, which reduces the overall carbon footprint of the production process.
- Waste Reduction Technologies: Technologies such as precision filling systems help minimize waste by ensuring the correct amount of liquid is dispensed every time.
- Sustainable Materials: Machines made from recyclable and eco-friendly materials contribute to a greener production environment.
By implementing these sustainable practices, companies can reduce their environmental impact and align with industry standards for environmentally responsible manufacturing.
Liquid filling machines are essential for modern production processes in industries ranging from food and pharmaceuticals to cosmetics and chemicals. With advancements in automation, efficiency, and sustainability, these machines continue to play a crucial role in enhancing production quality, safety, and environmental responsibility. By investing in the right liquid filling technology, businesses can not only improve their production processes but also meet the demands of today’s fast-paced and eco-conscious markets.
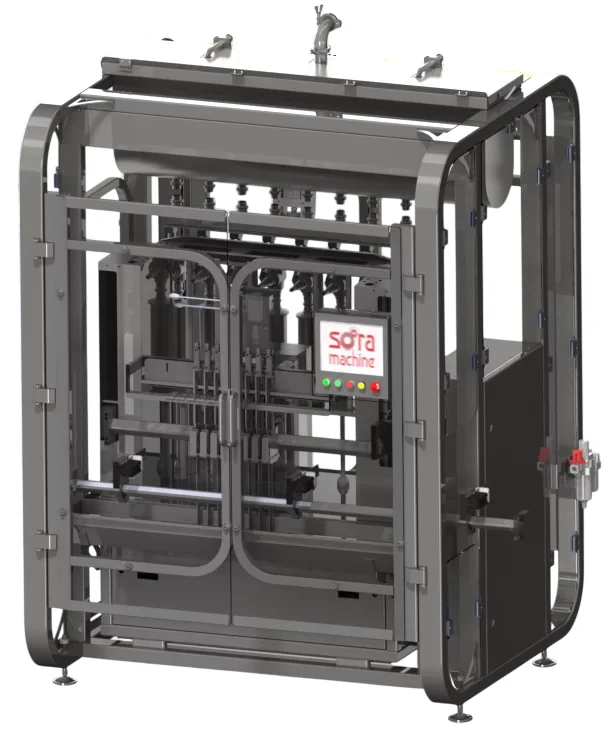