Keeping Your Line Alive, Efficient, and Problem-Free
When it comes to aerosol filling machines, performance isn’t just about what you see on day one—it’s about how that machine performs year five, year ten. The truth? Even the most advanced systems break down without the right care. And downtime? It’s not just annoying—it’s expensive.
Here’s how to actually keep your line running smoothly and your machines aging like fine wine (instead of rusting like forgotten gym equipment).
Why Should I Perform Regular Maintenance on My Aerosol Filling Machines?
It’s simple: no maintenance, no reliability.
Aerosol filling machines are precise systems. They deal with pressure, flammable materials, crimping tolerances, and moving components that don’t forgive neglect. Regular maintenance ensures one thing above all—predictability.
We’ve seen too many lines go offline because of one faulty valve, one ignored leak, one clogged nozzle. These aren’t big things. But they cause big trouble.
Regular care is your cheapest insurance policy.
How Should I Create a Daily and Weekly Maintenance Checklist for My Aerosol Filling Machines?
Keep it simple. Keep it consistent.
Daily Checklist:
- Clean all nozzles and valves post-shift
- Check pressure levels and air leaks
- Confirm actuator movement is smooth
- Visually inspect all pneumatic lines
- Empty waste or catch trays
Weekly Checklist:
- Lubricate moving parts as per OEM guide
- Check crimping head alignment
- Test fill accuracy on random samples
- Inspect sensors and safety switches
You don’t need to overcomplicate it. The key is routine. Machines love routine.
Which Monthly and Annual Maintenance Procedures Should I Apply to My Aerosol Filling Machines?
This is where you go deeper. Think prevention instead of reaction.
Monthly:
- Replace wear parts: O-rings, seals, and gaskets
- Deep clean the filling station components
- Test emergency stop systems
- Backup machine settings and diagnostics
Annually:
- Full service by certified technicians
- Calibration of dosing and pressure systems
- Upgrade control software if available
- Check frame integrity and support elements
Annual maintenance should feel like a reset. Do it right, and your machine feels new again.
What are the Most Common Problems Encountered in Aerosol Filling Machines and How Can They Be Solved?
Here’s the short list we run into (a lot):
- Inconsistent fill levels? → Likely a worn-out valve or contaminated nozzle.
- Crimping defects? → Check alignment and tightness—don’t force your tooling.
- Gas leaks or weak sprays? → Might be a can valve compatibility issue.
- Actuator misfires? → Solenoid or timing delay. Recalibrate.
Most of these problems don’t require an engineer. They require someone who knows what “normal” looks like. Train your eyes. Your ears. Your gut.
How Should Operators Be Trained for the Correct and Long-Lasting Use of My Aerosol Filling Machines?
Let’s be real—your aerosol filling machine’s lifespan is only as good as the person operating it.
Every operator should know:
- How to recognize early failure signs
- What not to touch when there’s an issue
- How to reset or shut down the machine safely
- Where to report even the smallest irregularity
Most breakdowns come from this: someone didn’t want to “bother” maintenance. That mindset kills machines. Train ownership, not just usage.
Which Long-Term Strategies Should I Follow to Maximize the Lifespan of My Aerosol Filling Machines?
Here’s the real gameplan:
- Build a preventive maintenance calendar that includes everything from cleaning to calibration.
- Stick to OEM parts. They’re not upsells—they’re life insurance.
- Document everything. Date of service, problem reported, solution applied. If it happens twice, it’s a pattern.
- Train new operators properly—no machine is plug-and-play, even if it looks like it.
- Invest in spare part kits. You don’t want to wait 6 weeks for a €4 part to arrive from Europe.
Your filling machine doesn’t just need to run. It needs to run right—for years. And you control that more than you think.
Aerosol filling machines are long-term players. They’ll stick with you through new SKUs, market shifts, and wild production schedules—if you treat them right.
Maintenance isn’t optional. It’s strategic.
So ask yourself: Am I reacting to problems, or preventing them altogether?
We’ve helped plenty of manufacturers overhaul their maintenance game—drop a message if you’re tired of breakdowns and want something that actually lasts.
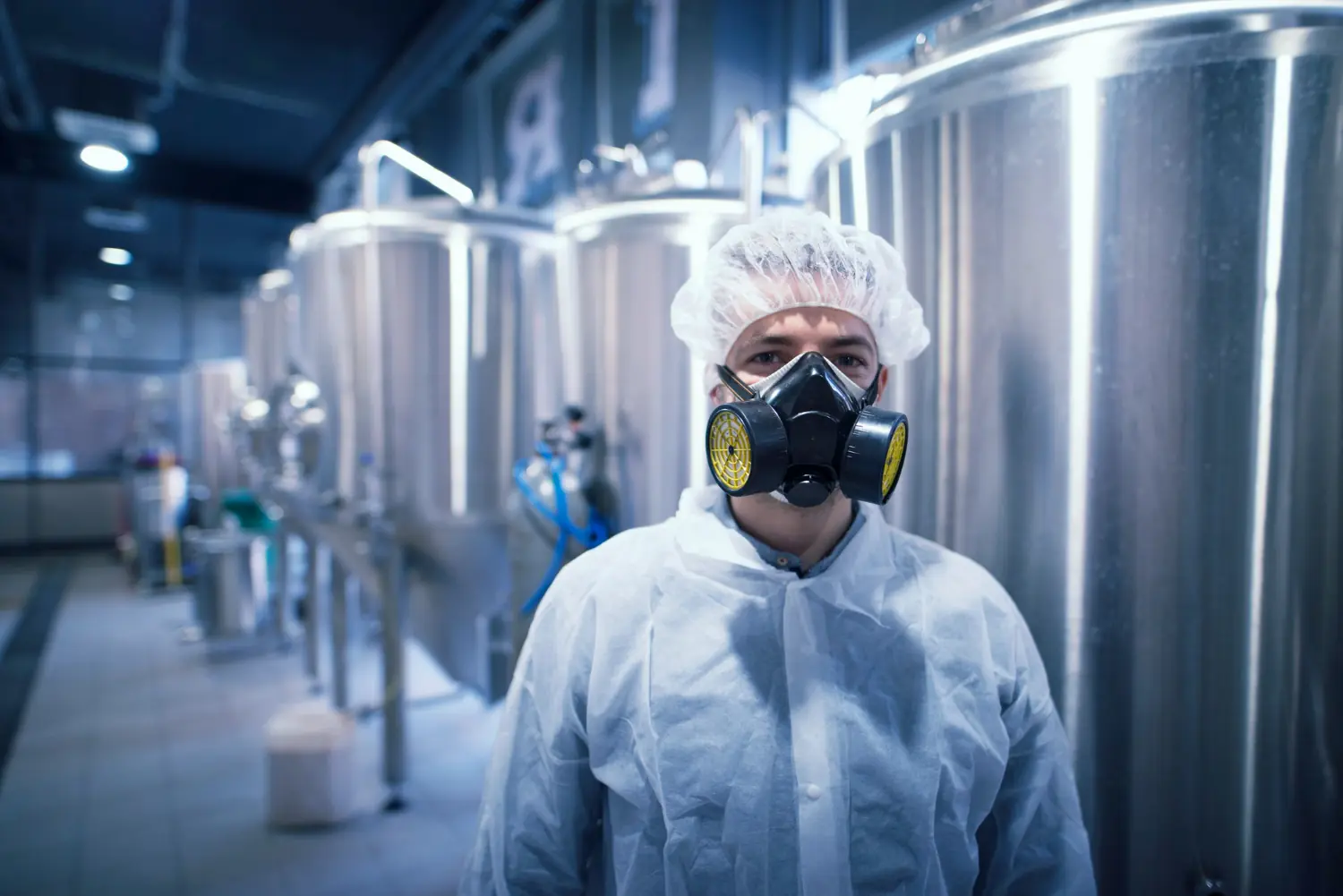