Leak testing is a series of control processes carried out to understand whether the pressurized content inside aerosol cans is escaping. The main purpose of this test is to:
- Ensure product safety
- Guarantee content stability
- Detect production errors before reaching the user
What Problems Arise if Leak Testing is Not Performed?
Skipping or superficially performing the leak test carries the following risks:
- Formation of Explosive Atmosphere: Especially in products containing flammable gases such as LPG, propane, or butane, leakage can lead to the formation of an explosive gas/air mixture in the environment.
- Self-Discharge: Even a small leak in the valve or gasket can cause the product to empty itself over time.
- Loss of Consumer Confidence: An aerosol product that is empty or does not spray upon initial use seriously damages trust in the brand.
- Legal and Financial Sanctions: Recalls, penalties, and potential compensations can cause significant damage to companies.
What Methods Are Used in Leak Testing?
The appropriate test method may vary for each production line. Commonly used leak testing methods include:
- a. Water Bath Method: The can is immersed in a water-filled tank. Bubbles indicate a leak. It is a simple and visual method.
- b. Vacuum Test Chamber: The product is tested under low pressure. Leaks are detected more quickly in this environment.
- c. Testing with Mass Spectrometer: Gas leaks can be detected even at very sensitive levels through special detectors. It is generally used for medical products.
- d. Ultrasonic and Laser Systems: Allows for high-speed leak detection in automatic production lines. It is contactless and minimizes operator error.
When and at What Stage Should Leak Testing Be Performed?
Correct timing directly affects the effectiveness of the test. Leak testing is generally applied in two stages:
- After Filling / Before Labeling: The ideal time to sort out defective products.
- Random Sampling Before Shipment: Used to detect damage that may occur during transportation.
Some manufacturers even apply pre-tests after can production, aiming for zero defects.
Which Regulations and Standards Mandate Leak Testing?
Many regulations worldwide mandate leak tightness control for aerosol products. Some examples:
- ADR (European Agreement concerning the International Carriage of Dangerous Goods by Road): Leak tightness is a prerequisite for the transportation of dangerous goods.
- FDA (Food and Drug Administration): Mandates leak testing, especially for pharmaceutical and cosmetic products.
- ISO 9001 / ISO 22716: It is necessary to carry out controls to ensure product safety in quality management systems.
These regulations cover not only the manufacturer but also the distributor and exporter.
What is the Impact of Leak Testing on the Brand?
Reliability is the most important value of a brand. Leaking or defective aerosol products can lead to the following damages:
- Negative reviews on social media and e-commerce platforms
- Product returns and customer loss
- Recall operations
- Loss of brand value in the long term
Each of these creates much greater damage than the cost of testing.
Should Leak Tests Be Automatic or Manual?
Manual tests may be suitable for low-volume production. However, automatic systems are preferred for high-volume production for the following reasons:
- Speed: Hundreds of products can be tested per minute.
- Consistency: The risk of human error is reduced.
- Data Recording: Test results can be stored digitally.
What Challenges Are Encountered Regarding Leak Testing?
Some problems may be encountered in the implementation of leak testing:
- Insufficient Calibration: Devices giving incorrect readings.
- Failure to Detect Micro-Leaks: Leaks that may be harmful, especially in the long term, may be overlooked.
- Lack of Operator Training: Incorrect application of the test can lead to erroneous results.
For this reason, regular training and maintenance are required for both equipment and human resources.
How Can the Leak Testing Process Be Optimized?
The following steps can be taken to optimize leak testing in your production line:
- Risk-Based Approach: Determine which products require more testing.
- Data Collection: How many products are leaking? At what stage does the error occur? Track these.
- Process Automation: Standardize the process with appropriate testing devices.
- Training: Ensure that operators are proficient in the testing process.
In this way, the testing process becomes both effective and sustainable.
Leak Testing is Not a Luxury, But a Necessity
Every process performed in the aerosol filling line determines the quality of the final product. However, leak testing is at the center not only of quality but also of safety and responsibility. Therefore, this test should not be an option but an integral part of the production process.
Thanks to developing technologies, it is now possible to perform more sensitive, faster, and more reliable leak tests. It should not be forgotten that the safety of products directly affects not only consumer satisfaction but also the future of the brand.
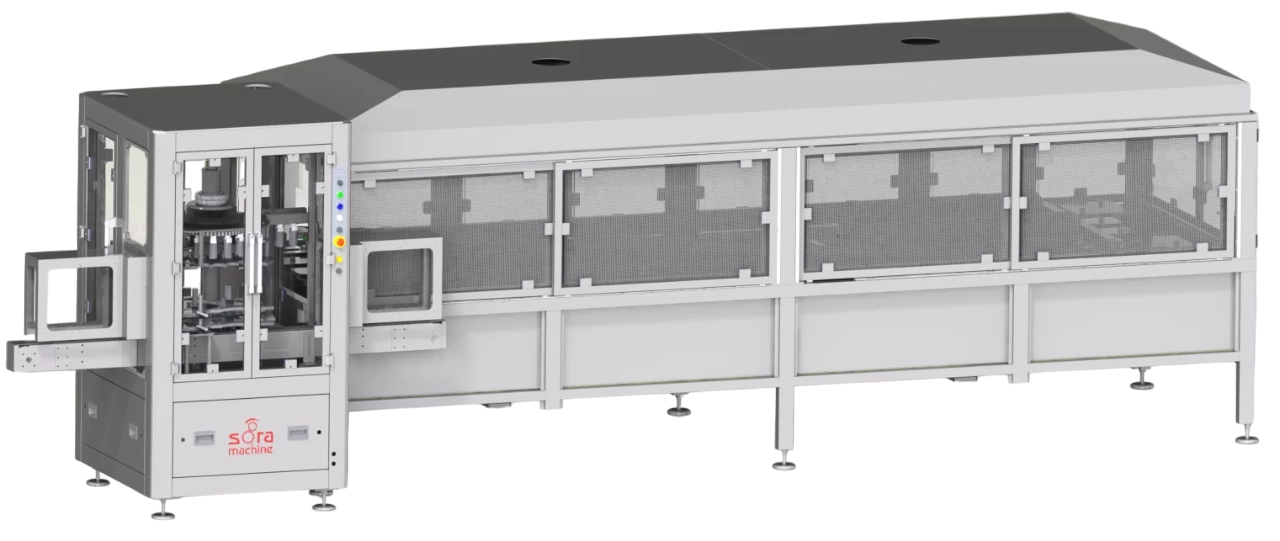